Industrial Visit – Rigen Packaging
Industrial Visit – Rigen Packaging
Summary
Event Name: Industrial Visit – Rigen Packaging
Objective: The purpose of the industrial visit is to provide students real-world exposure to operational procedures and practical insights into the field, which gives them an in-depth understanding of theoretical concepts through real-world exposure.
Outcome: The visit enabled students to apply theoretical concepts learned in the classroom to real-world scenarios, particularly observing how management principles are implemented in a company undergoing ISO Audit preparation in the Packaging sector.
Report
The Operations club of Symbiosis Institute of Business Management, Hyderabad, organized an Industrial Visit for the MBA – Operations, Human Resource and Finance students (Batch 2022-24 and Batch 2023-25) on 4 th January, 2024. Upon arrival at Rigen Packaging, Mr. Nageshwaram, the Quality Manager, gave the students a brief introduction about the company and an overview of the factory’s operations.
Rigen Packaging stands as a premier artisan, skilfully producing refined gadget enclosures and flexible packaging for various companies. The company's dedication to excellence is unmistakable, harmonizing functionality and aesthetics with a seamless precision that defines each product as a testament to both sophistication and practicality.
The Corporate is engaged in the business of manufacturing including production and processing, importing, paper, trading, buying, selling, exporting and/or otherwise dealing in all types of flexible packaging materials, printed and un-printed lamination and is currently preparing for its ISO Audit.
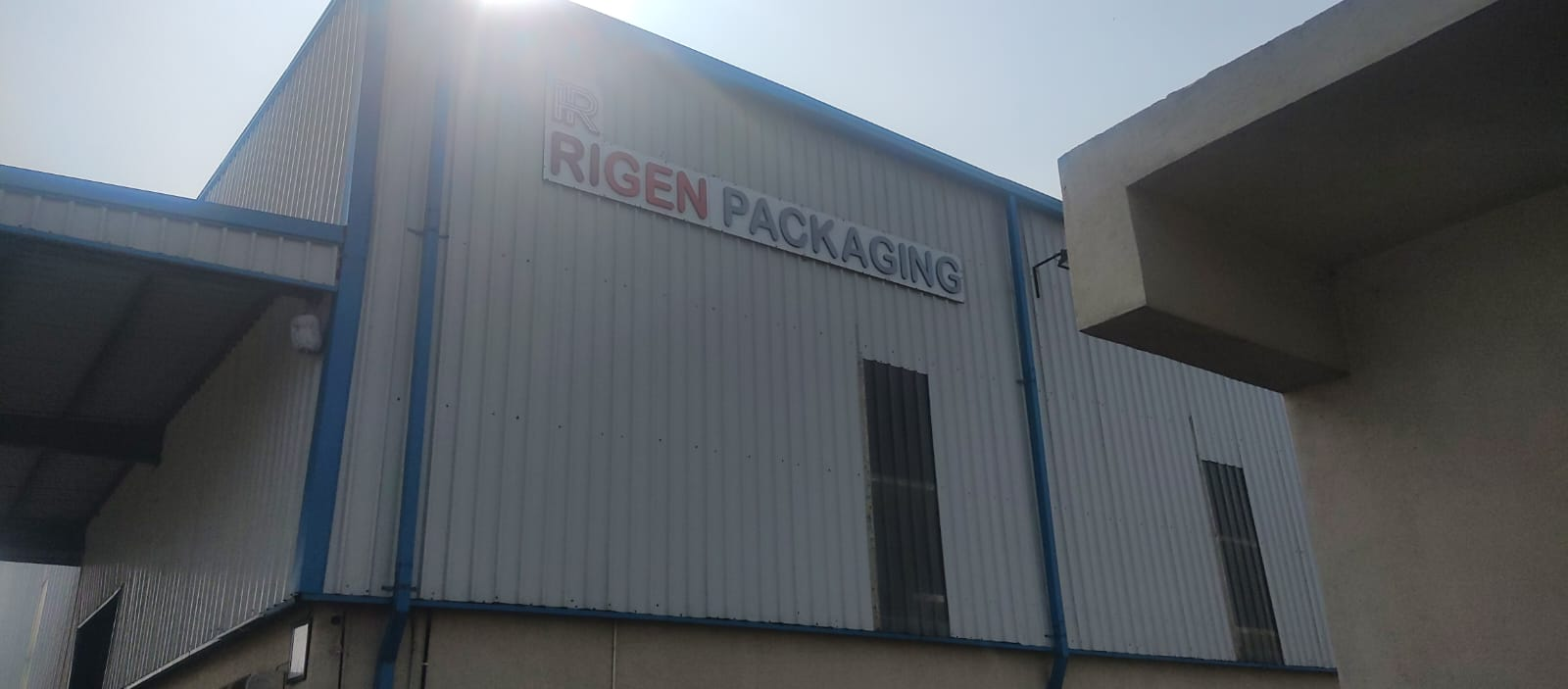
OPERATIONS
During the visit, there were various operations involved from procurement of raw materials to packaging and storing;
Obtaining the Raw Materials-
Rigen begins manufacturing by carefully sourcing raw materials from multiple vendors, including cardboard, plastic, and paper. These materials are kept in a regulated atmosphere to maintain quality and guard against any potential damage. To preserve their integrity and prevent potential damage, these materials find a secure abode in a controlled environment, setting the foundation for a seamless and efficient production process.
Design and Pre-Press-
Rigen has a dedicated pre-press section for customers looking for custom packaging solutions. Here, intricate designs are conceptualized. During the visit, the company were manufacturing laminated covers for a soap company. The expertise extends to the meticulous preparation of printing plates, tailored to meet the unique requirements of each project.
Printing-
The next step is to print designs onto the raw materials using different printing methods like digital printing, offset printing, or flexography. Here, different coloured cylinders are used for different stations and the ink used for printing is mixed with thinner for dilution. Printing process occurs in phases where one phase is dedicated for printing of one colour only, then in the next phase a different colour is printed on the sheet.
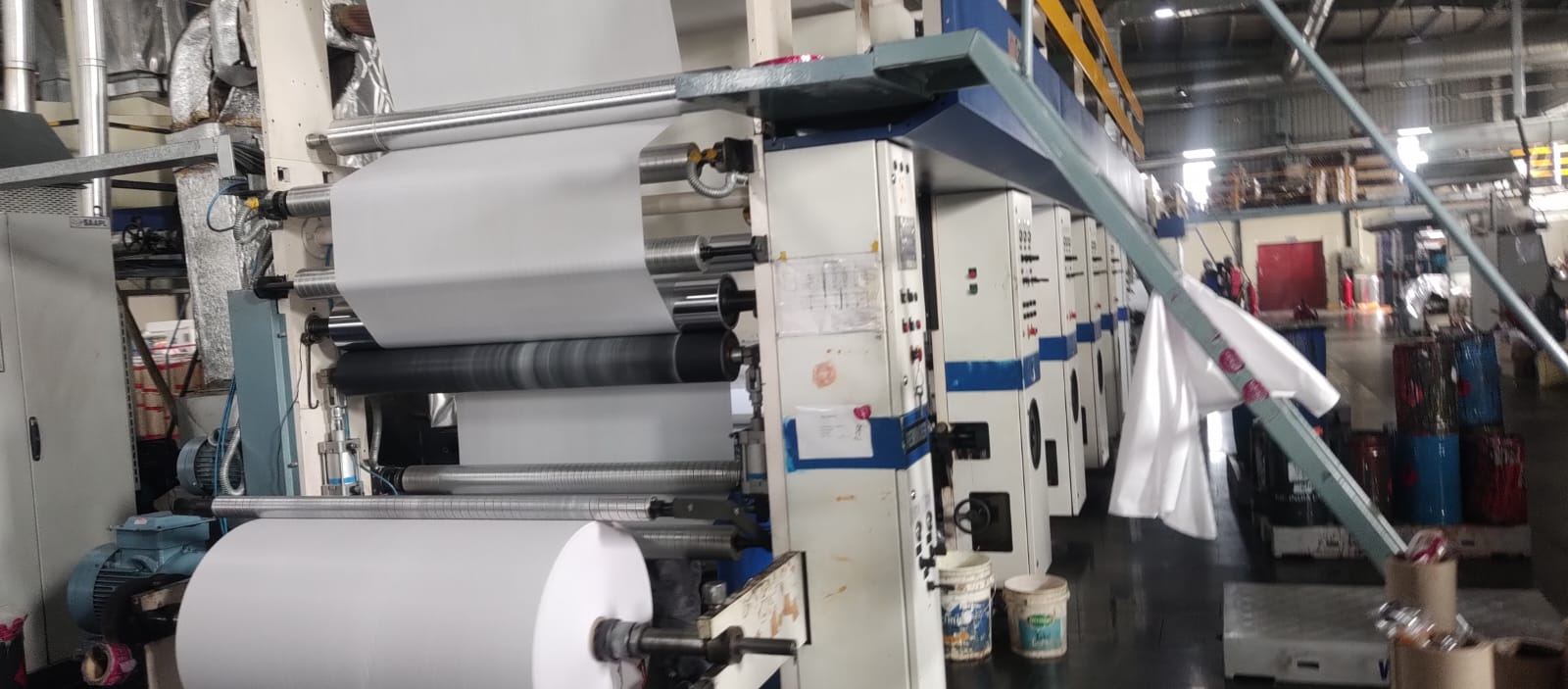
(Printing in process)
Flexi machine-
Flexographic printing, or Flexo as it is more commonly known, is a direct rotary printing process. Images are transferred from a flexible photopolymer relief plate onto a continuous substrate, which is supplied in reel form.
The process begins with plate preparation, where the desired image is intricately engraved. Application of ink is crucial; ink is uniformly transferred from a reservoir to the flexible printing plate using an anilox roller with etched cells. The pattern is transferred onto materials such as paper, film, or cardboard when the substrate passes through the press and makes contact with the inked plate. After printing, drying is an essential step. The substrate is passed through a drying system where the ink is set and solidified using heat or UV curing. many printing units are frequently seen in flexo machines, which enable the application of many colours in a single run.
Flexo printing is a highly efficient printing technique that is well-suited for high-volume jobs. Its versatility in handling various substrates preferred in jobs like packaging here at Rigen Packaging that demand high-quality prints at a reasonable price.
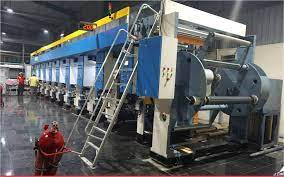
Combi machine-
A combi packaging machine is a small, multipurpose gadget that combines several packaging operations into one cohesive system. Mainly used for lamination purposes in the Rigen factory. These devices frequently have facilities for cartooning or boxing, which gives the packaged goods an additional degree of protection. Functions related to sealing and labelling provide safe closures and offer crucial branding or product information.
Some combi packaging machines even extend their capabilities to include palletizing to help with organised storage and transportation. Combi packaging machines, which are renowned for their effectiveness and ability to maximise space, are essential in sectors including food and beverage and medicines.
Assembly and Finishing-
Additional procedures like laminating, coating, gluing, and hot stamping are used to improve both appearance and functionality. Boxes, inserts, labels, and other packing components are carefully assembled during the assembly stage. Wax is also used to make the soap unstick able to the wrapper during storage. Lamination was done with the help of a Combi machine. The assembly process intricately brings together different components, such as boxes, inserts, and labels, ensuring that each detail aligns seamlessly with the envisioned design and meets the highest quality standards.
Quality Control-
At each juncture of the production process, Rigen enforces stringent quality control measures. This ensures not only consistency in the manufacturing process but also adherence to the precise specifications outlined by the customers. This phase represents a meticulous checkpoint, safeguarding the reputation of Rigen's craftsmanship. Quality standards for ink in use at Rigen Packaging particularly need to have a viscosity of 14 to 17 Poise.
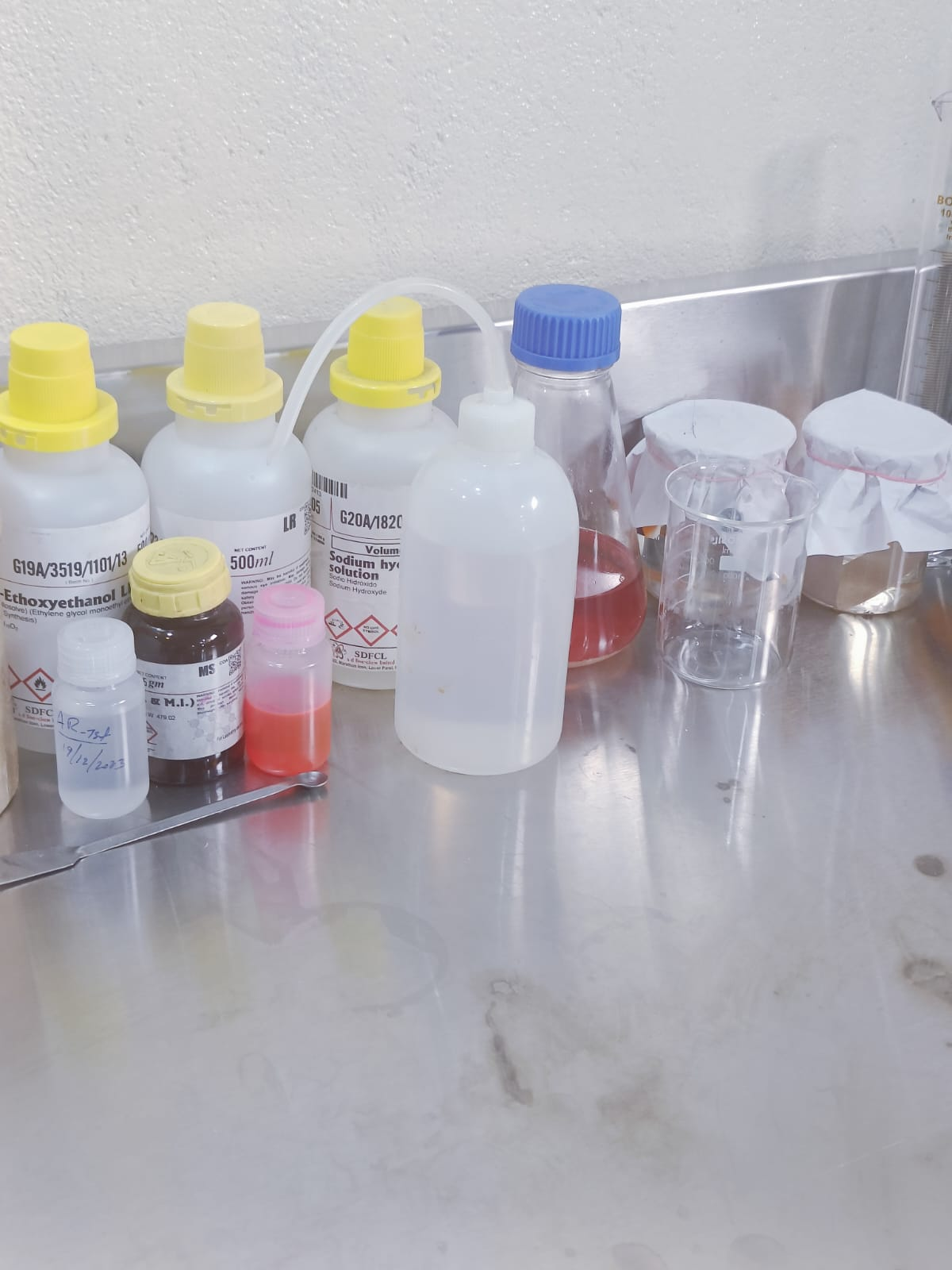
(Quality control measures)
Storage-
After packaging is finished, it is kept in a small warehouse until the next stage of the production process. Beyond mere storage, the company also makes sure of the strategic organization, ensuring that products are readily accessible and primed for the subsequent stages of the production cycle.
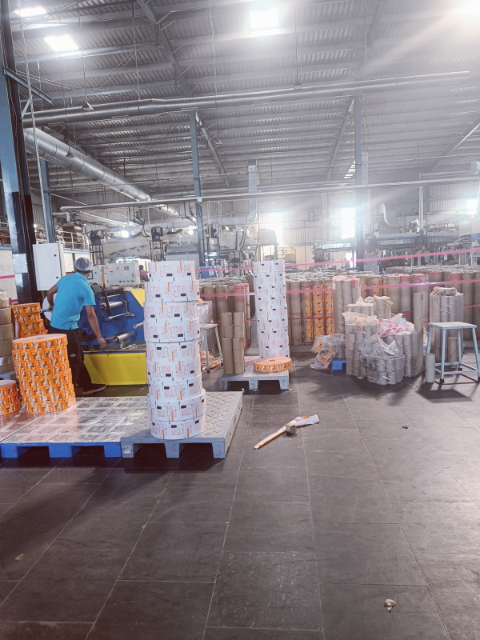
(Storage of the finished goods)
Delivery-
The thorough delivery of completed packaging to clients is the last phase in Rigen's extensive and quality-driven production process. This step marks the culmination of Rigen's comprehensive and quality-driven production process, ensuring customer satisfaction from creation to delivery.
This visit provided student with a hands-on understanding of the Total Quality Management, Logistics Management and Manufacturing employed by Rigen Packaging Pvt Ltd in its day-to-day operations.
FINANCE
During the Finance batch visits of 2022-24 and 2023-25 it was observed that Rigen Packaging, an unlisted private company, consistently produces an average of 480 kilograms of products daily, operating margin of Rigen packaging is 30-35%. The authorised share capital of 1 lakh INR is the same as the entire paid-up capital of the company. Realising the need of accurate accounting, Rigen Packaging keeps a thorough ledger to track and record every facet of its business activities.
Every day, the facility produces flexible packaging for a wide range of customers, including well-known businesses like Wipro and Santoor soap. Rigen Packaging carefully keeps track of and documents information about production quantities, necessary supplies, and the performance of operating machinery in order to guarantee smooth operations. This dedication to monetary transparency and record maintenance underscores Rigen Packaging's dedication to operational excellence, providing a robust foundation for its continued success in the dynamic packaging industry.

HUMAN RESOURCES
The introduction of the batches to the factory staff was handled by the Quality manager of Rigen packaging, there he welcomed the students to the factory and gave a brief about the staff and the history of the company.
Observations revealed the HR team's strategic approach to hiring, emphasizing a tailored selection process to find the right individuals for manufacturing roles. During the visit, it was evident how actively the HR team trains employees to be excellent in their professions and adjust to changes in the sector. The group's dedication to honing their skills was clear. Furthermore, a careful examination of performance management demonstrated their commitment to guaranteeing effective and high-quality work.
In summary, the factory tour provided students with a comprehensive understanding of how Rigen Packaging, backed by a robust HR strategy, not only manages production efficiently but also places significant emphasis on the growth and welfare of its employees.
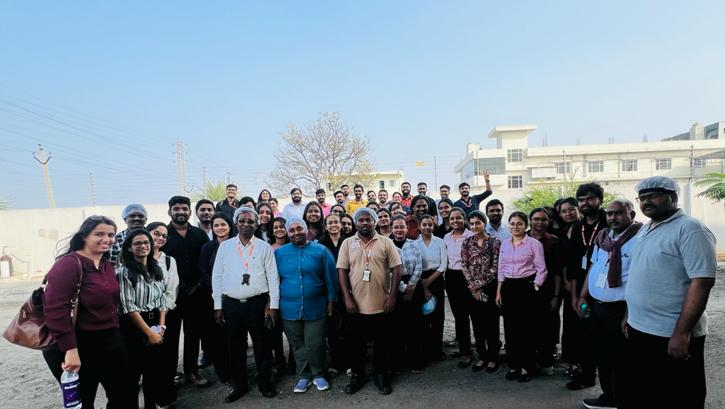
(HR and Operations students with teacher in-charge and Rigen Packaging staff members)
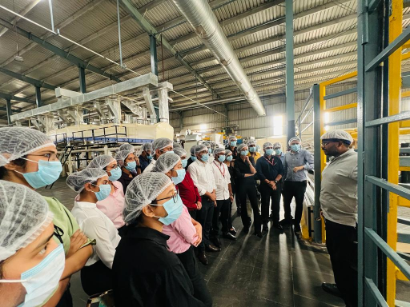
(Introductory meeting)
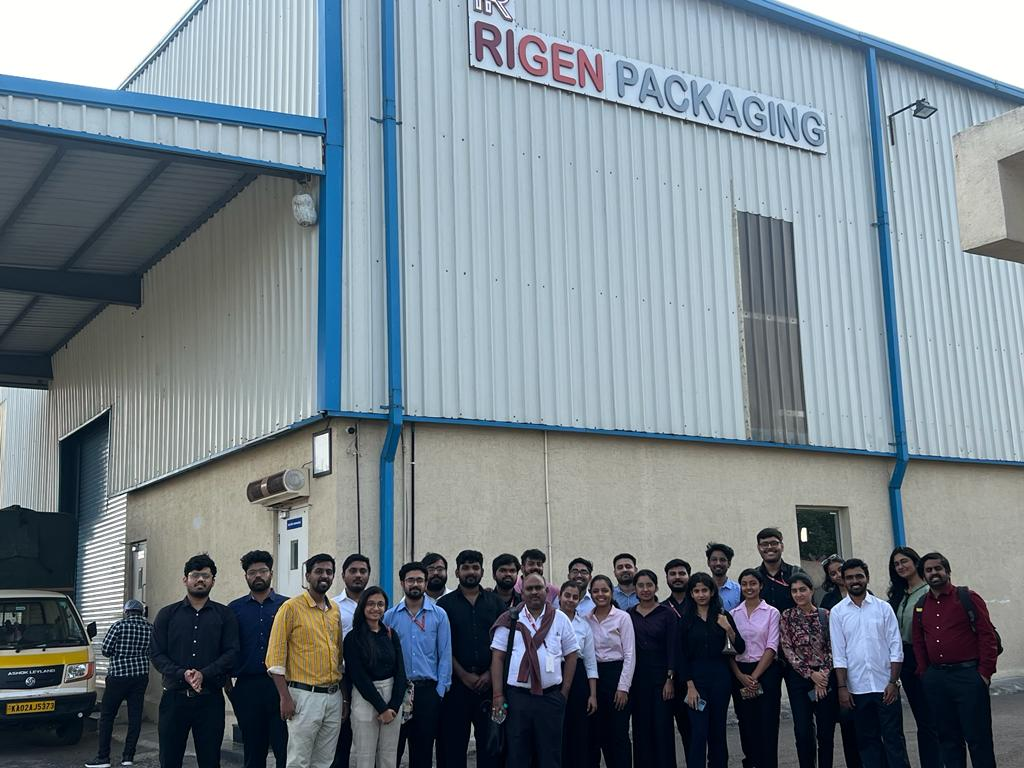
(Operations student group photo with faculty in-charge)